PP-R product line is run Ningbo KonRun Machinery Technology Co., Ltd. developed using the latest technology, high efficiency, reduce production costs. Screw barrel structure of the host unique design, with IKV forced feeding structure and the perfect combination of downstream equipment, so that the entire production line really highly efficient and stable high-speed extrusion line.
Ppr Pipe Extrusion Machine,Ppr Pipe Production Line,Ppr Pipe Extrusion Line,Ppr Pipe Extrusion Making Machine KonRun Intelligent Machinery(Ningbo) Co., Ltd. , https://www.konrunmachine.com
Brass or Stainless Steel in High-Pressure Hydraulics
# Choosing Between Brass and Stainless Steel in High-Pressure Hydraulic Systems
In the complex world of hydraulic engineering, selecting the right material is crucial, especially when dealing with high-pressure systems. Among the various options available, brass and stainless steel often stand out as top contenders. Each material has its own set of properties that make it suitable for particular applications. But how do they hold up under the intense demands of high-pressure hydraulic operations? This exploration delves into the strengths and weaknesses of brass and stainless steel within such rigorous conditions.
## The Importance of Material Selection in Hydraulics
The choice of material in hydraulic systems goes beyond mere compatibility with fluids or cost-effectiveness. It’s about ensuring the system can endure the immense pressures it will face while maintaining its integrity over time. A material’s ability to withstand operational pressures, resist wear, and prevent corrosion is vital for ensuring safety, efficiency, and long-term reliability in hydraulic systems.
## Brass: A Reliable Option for Moderate Pressures
Historically, brass has been valued for its excellent corrosion resistance and ease of machining. It is frequently used in hydraulic systems operating under moderate pressures. Typically, brass fittings and components can handle pressures ranging from 1,000 to 3,000 PSI. However, under extremely high-pressure conditions, brass tends to show its limitations. With a relatively lower tensile strength, brass is more susceptible to deformation and failure when subjected to intense stress. While certain specialized brass alloys and designs can handle pressures slightly above this range, brass generally isn’t recommended for the highest-pressure applications.
- **Common Uses:** Brass is widely used in low to moderate-pressure hydraulic systems.
- **Pressure Range:** Standard brass components typically operate within 1,000 to 3,000 PSI.
- **Limitations:** Brass struggles under extreme pressures, leading to potential failures.
## Stainless Steel: The Champion of High-Pressure Systems
Stainless steel, on the other hand, is renowned for its strength and resilience. It excels in high-pressure environments, thanks to its high tensile strength and exceptional corrosion resistance. Stainless steel components can handle pressures ranging from 5,000 to 6,000 PSI, with high-grade stainless steel and specially designed components capable of withstanding pressures exceeding 10,000 PSI. This makes stainless steel the go-to choice for critical applications in industries such as aerospace, maritime, and heavy machinery.
- **Versatility:** Stainless steel is ideal for medium to high-pressure hydraulic systems.
- **Performance:** Standard stainless steel components can manage pressures up to 6,000 PSI, with premium grades exceeding expectations.
- **Durability:** Stainless steel’s robust nature ensures prolonged service life and reduced maintenance costs.
## A Comparative Look: Brass vs. Stainless Steel
When comparing brass and stainless steel under high-pressure scenarios, several key factors emerge:
- **Tensile Strength:** Stainless steel outperforms brass, offering greater resistance to deformation and failure.
- **Corrosion Resistance:** Both materials provide good corrosion protection, but stainless steel’s broader resistance gives it an edge.
- **Longevity:** Stainless steel’s superior strength translates to longer component lifespans and fewer replacements.
## Real-World Applications and Insights
From deep-sea exploration tools to industrial machinery, stainless steel dominates high-pressure applications across numerous industries. Brass, meanwhile, finds its niche in less demanding environments where pressure levels don’t pose a threat to its structural integrity. Case studies from sectors like aerospace, maritime, and manufacturing provide concrete evidence of how these materials perform under real-world conditions.
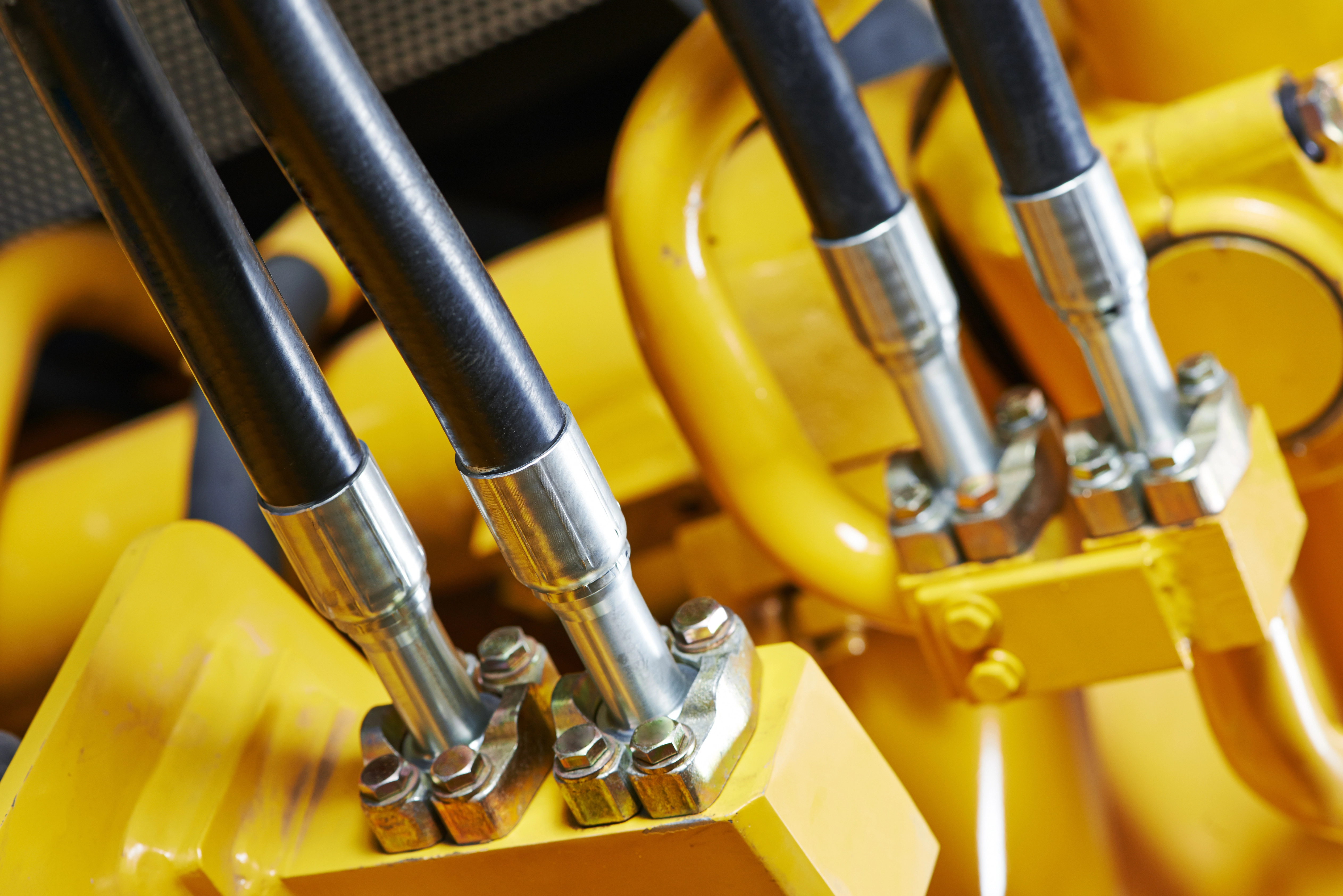
## The Financial Consideration
Deciding between brass and stainless steel involves more than just technical specifications—it’s also a financial decision. Brass is often favored in budget-constrained projects due to its lower upfront cost. However, when considering the potential risks and long-term maintenance associated with high-pressure systems, investing in stainless steel can prove more economical over time through increased durability and reliability.
## Conclusion: Balancing Needs and Costs
Selecting the correct material for high-pressure hydraulic systems requires balancing technical requirements, financial considerations, and specific application needs. While stainless steel remains the preferred choice for demanding environments, brass continues to serve well in moderate-pressure scenarios where cost constraints are a priority.
## Ensuring Long-Term Success
To maximize performance, regular maintenance, adherence to operational guidelines, and consideration of environmental factors are essential. Understanding the unique demands of your hydraulic system will help you make the most informed and effective material selection.
## Frequently Asked Questions
**Q: How does the cost of brass compare to stainless steel in hydraulic systems?**
A: Brass components are generally cheaper initially, but stainless steel proves more cost-effective in the long run due to its durability and reduced maintenance needs.
**Q: Which material is better suited for high-temperature hydraulic applications?**
A: Stainless steel handles high temperatures more effectively than brass, maintaining its strength and integrity even under extreme thermal conditions.
In conclusion, whether you opt for brass or stainless steel depends largely on your specific needs and constraints. By carefully evaluating these factors, you can ensure your hydraulic system operates safely and efficiently under any pressure.